GE Healthcare opens its first Eu 3D printing and design centre
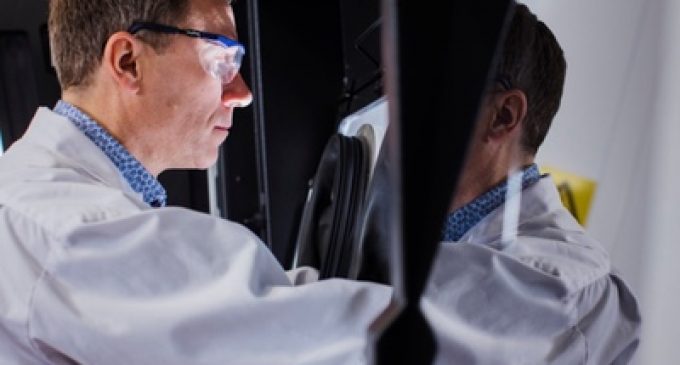
A 3D printed part can combine 20 parts into a single part and improve performance, reducing parts in a manufacturing process could benefit the biomanufacturing industry where processes and equipment are incredibly complex and made up of hundreds of parts.
GE Healthcare has opened its first 3D printing lab, called the Innovative Design and Advanced Manufacturing Technology Centre for Europe, in Uppsala, Sweden. The centre will use technologies including 3D printing and robotics to speed up the launch of new innovative products for the healthcare industry.
The centre combines advanced manufacturing technology such as metal and polymer printers and collaborative robots, or ‘cobots’, with traditional machining equipment.
A key in realising the advantages of 3D printing is ensuring the technology is considered at the start of the innovation process with R&D teams working with advanced manufacturing engineers and in collaboration with customers.
The new centre in Uppsala will ensure additive expertise is available from the start of product design. Teams will design, test and produce 3D printed parts for GE Healthcare products and prepare for final transfer to manufacturing.
Advanced manufacturing techniques like 3D printing can bring significant benefits to manufacturing processes. For example, a 3D printed part can combine 20 parts into a single part and improve performance.
Reducing parts in a manufacturing process benefits industries like the biomanufacturing industry where the processes and manufacturing equipment are complex and made up of hundreds of different parts.
Andreas Marcstrom, Manager of Additive Engineering at GE Healthcare’s Uppsala site, said: “We are exploring opportunities where additive engineering can bring cost savings and technical improvements to our supply chain and products. Simply printing a part does not really deliver that much improvement to a product or process. You have to re-think the entire design — to do this, you need your R&D teams and your additive manufacturing engineers working from the start of the development process — our centre in Uppsala ensures that critical step.”
GE is working with the biotechnology company Amgen to test the performance of a chromatography column, used in the complex process to develop biopharmaceuticals, a range of drugs used to treat diseases including cancer and immune diseases.
The 3D printed column has been custom-designed and is now being tested to see if it can be used in Amgen’s research to help develop improved processes for the purification stage of biopharmaceutical production.
The GE Healthcare Advanced Manufacturing Engineering team have also developed and programmed multiple cobots, which are now installed across GE Healthcare factories globally and are improving efficiency in production lines.
Many are part of GE Healthcare’s development of Brilliant Factories — plants that combine continuous improvement and digital to operate more efficiently and with higher quality.
The centre in Uppsala joins GE Healthcare’s other advanced manufacturing and engineering centre, which is based in Milwaukee, Wisconsin. The teams in Uppsala will collaborate with those at the Milwaukee centre, sharing knowledge and working on new design ideas.