Reduce SOP Complexity – Top 10 Tips
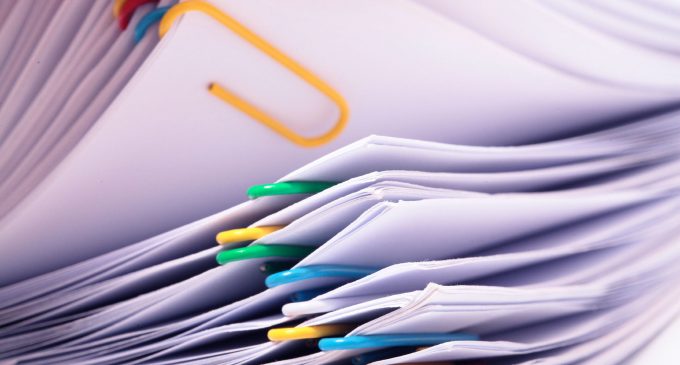
Standard operating procedures (SOP’s) define the essential steps, their order and the instructions necessary to formally repeat a quality performance. SOPs essentially are a blue print for risk mitigation. Industry has to improve control of their own processes with a focus not simply on compliance. Compliance demonstrates and documents adherence to a set of requirements dealing with the symptoms of a problem. Quality proactively deals with the problem itself.
Restructuring SOPs can seem expensive and complicated. However, this is inconsequential when compared with potential shutdowns or compliance problems due to poor and/or overly complex SOPs. The risks and potential business impact should not be undermined. The cost of non-compliance and of not optimising operational processes are real.
SOPs can be complex to create and maintain. However, regulatory bodies are becoming more and more focused on compliance and enforcement operations. Most SOPs are very complex and can be difficult to read and follow on a daily basis. Too much information and excessive detail increases the risk of errors and mistakes. Finding the balance of how much detail to include in an SOP and what to remove or leave out is difficult. Often, companies write their procedures by passing on the “how”, but not the “why”? Complexity leads to greater risk of error, demotivation and disengagement amongst personnel.
Top 10 Tips to reduce SOP complexity :
- Review the writer and the reviewers, the user should be the author of the procedure: However, the more you know in a certain field the harder it is to break information down. Either you give more information than a person needs to understand or too little. A new person or a fresh set of eyes can offer great perspective to the clarity of your SOP.
- Re-engineering your Procedures: This is the way to simplify and improve your work flow. Often, companies write their procedures by passing on the “how”, but not the “why”? If the procedure is not re-engineered periodically, staff are taught processes that solve issues that no longer exist. This can start with making a list of every single step in a work process from start to end. At each step of the SOPs carefully ask “why”.
- Red line the procedure in the field: This is a great way to test if they’re still relevant and whether they make sense. Use this time to take clear photos, that you can add into your documents. There can be huge benefit in carrying out a procedure out in the field and getting the process documented and recorded correctly.
- Maintain simplicity: Long, complex SOPs can be difficult to follow. Strive to keep your SOPs simple and easy to use while still ensuring all important steps are included. Break down complex tasks into smaller sub-steps.
- Photos / drawings: The majority of the human brain is dedicated to processing visual information. Make your procedures easy to understand by including photos, drawings and flow charts. Humans prefer visuals to text, so it makes sense to use more visual information to explain complicated information. Include illustrations, diagrams, flowcharts or other visual aids that can help with understanding.
- Reduce the number of people involved in the tasks: The more people you have involved in a task, the more chance there is for mistakes. By reducing the number of people involved in a task, you can greatly improve how quickly it can be done and ensure that it’s done correctly.
- Avoid CAPAs to “Update Procedure”: Investigate true root causes by applying the 5 Why approach to your deviations. Look to engineering solutions and permanent resolutions for issues.
- Consider your audience: Produce SOPs based on the education, experience, knowledge and abilities of the personnel who will use the SOP.
- Test and verify SOP function: Once the SOP is finished, test it with those individuals who will be most likely to use it. Have them follow the SOP from beginning to end to ensure the information is clear and that no steps have been left out. Consider bringing in other testers who aren’t familiar with the process and having them apply the SOP. Protect what you have simplified. Don’t let people put back in what you’ve taken out.
- Review and revise, as needed: Once the SOP has been in use for several weeks, ask for responses from those with direct experience using it. Ensure that the SOP is clear, accomplishes its purpose and is easy to read and use. Revise based on the feedback you receive.
A list of SOP’s required by the FDA, EU GMP and WHO for GMP activities – http://www.gmp-compliance.org/gmp-news/which-sops-are-required-by-gmp
By Ann McGee
Managing Director
McGee Pharma International